Quality Planning
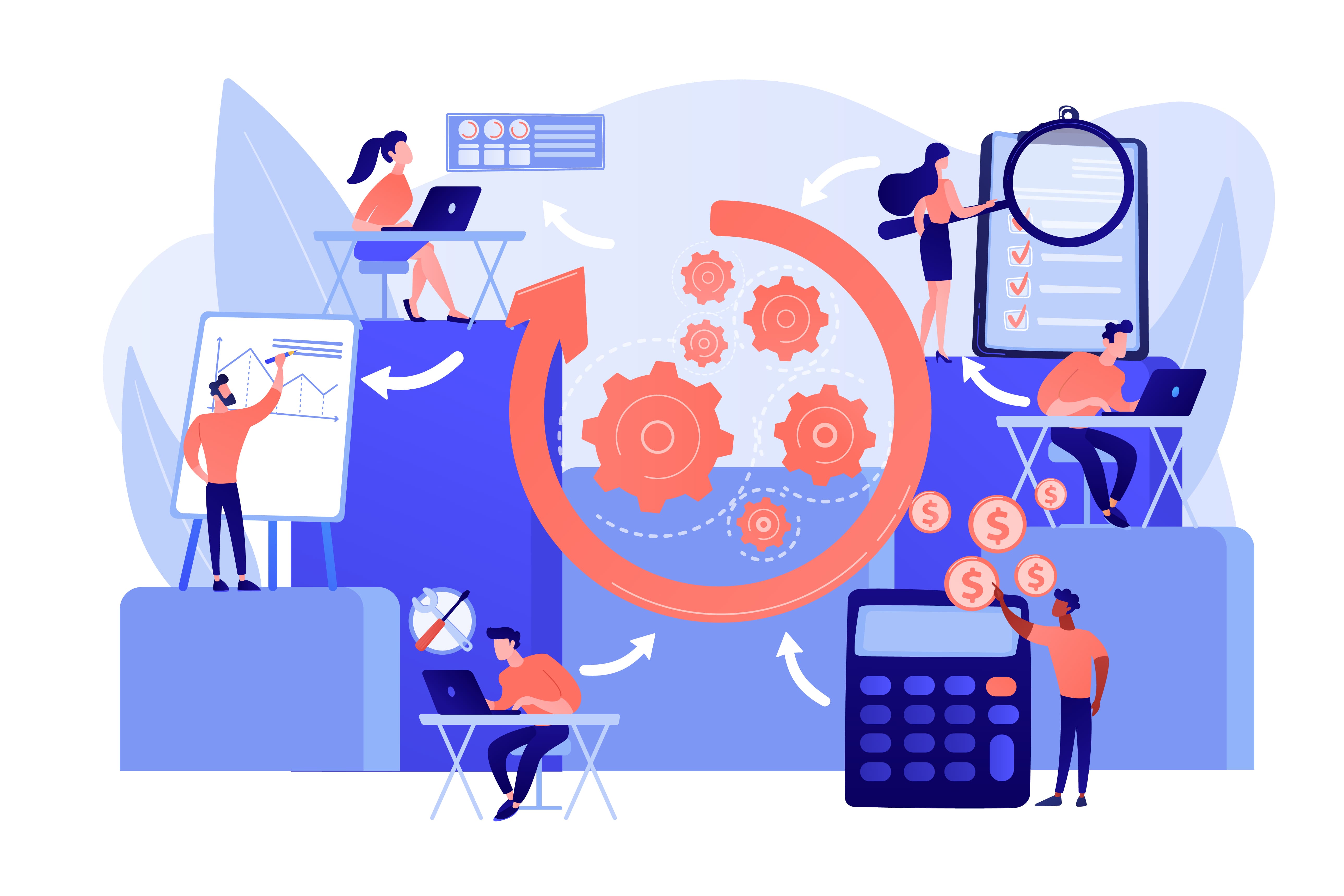
Quality Planning is a crucial step in project management that involves defining the quality requirements and standards for the project and developing a comprehensive quality management plan to ensure that project deliverables meet the desired level of quality.
Let’s explore the process in detail with an example:
Define Quality Requirements
In this step, the project team works closely with stakeholders to identify and document the quality requirements for the project. This includes understanding their expectations, needs, and any specific quality criteria that must be met.
Key activities in defining quality requirements are:
1. Stakeholder Engagement:
Engage with project stakeholders, including clients, customers, end-users, and subject matter experts, to understand their quality expectations and requirements.
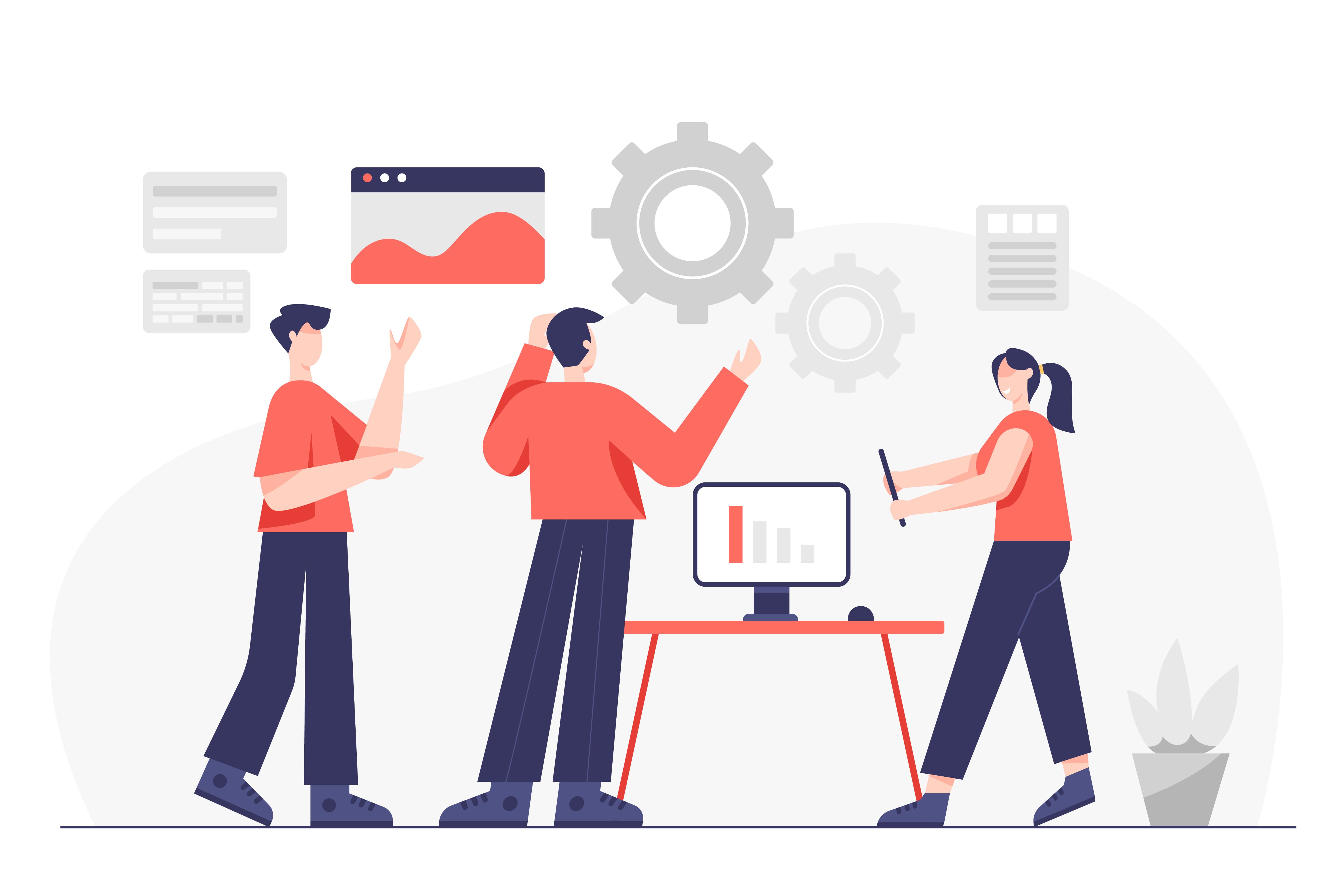
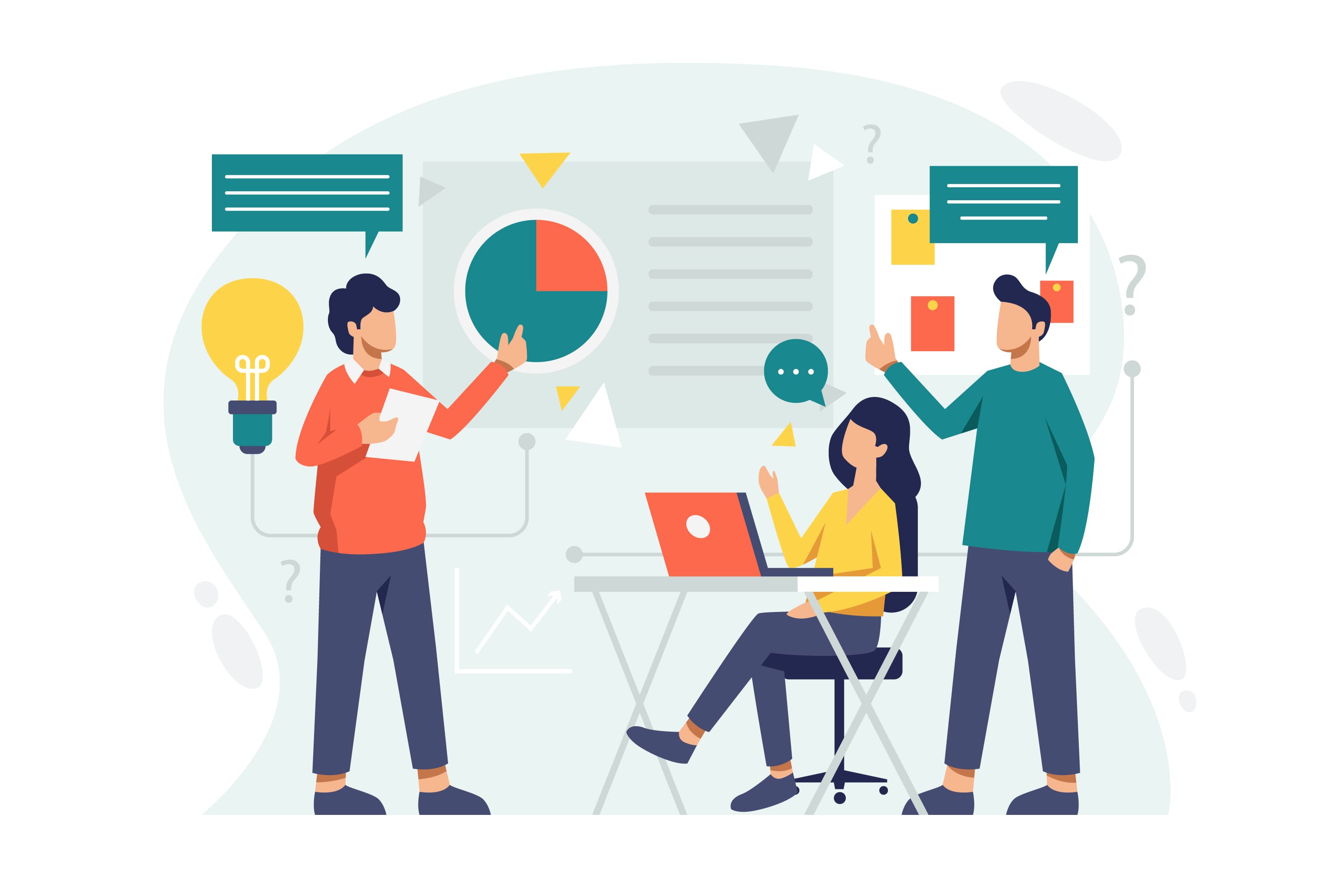
2. Identify Quality Criteria:
Determine the specific quality criteria that will be used to measure and assess the quality of project deliverables. For example, the criteria may include performance, reliability, usability, scalability, and compliance with industry standards.
3. Document Quality Requirements:
Document the identified quality requirements in a clear and concise manner, ensuring that they are measurable and aligned with project objectives. These requirements will serve as a reference throughout the project to ensure quality is maintained.
Let’s consider a construction project as an example:
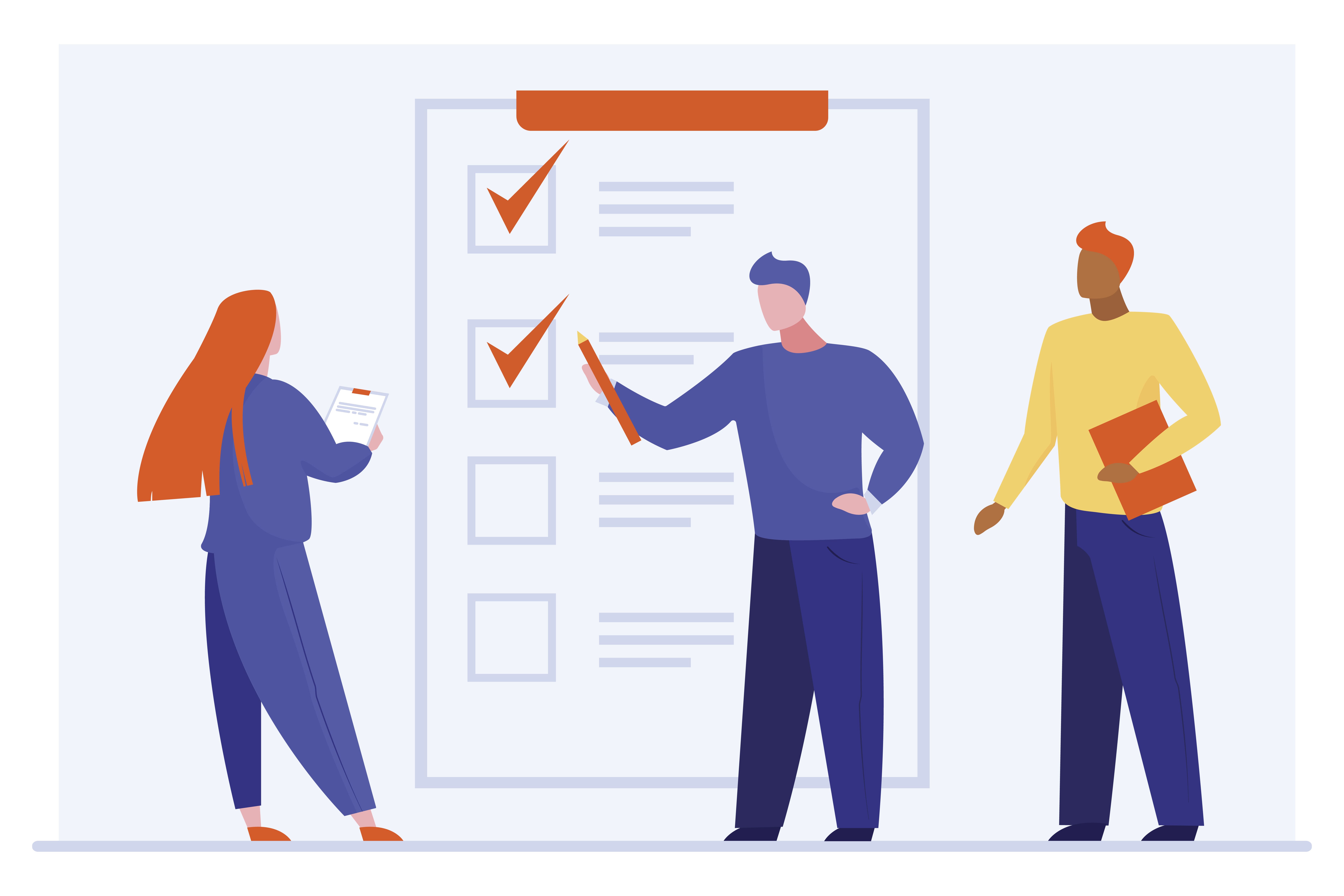
- Stakeholder Engagement: Engage with the client, architects, and engineers to understand their expectations and requirements regarding the quality of the construction project.
- Identify Quality Criteria: Determine criteria such as structural integrity, durability, aesthetic appeal, and compliance with building codes and regulations.
- Document Quality Requirements: Document the quality requirements, including measurable criteria such as the maximum allowable deviation in dimensions, acceptable material standards, and testing protocols.
Develop Quality Standards
Once the quality requirements are defined, the next step is to establish quality standards that will serve as benchmarks for measuring the quality of project deliverables.
This involves:
1. Research Industry Standards:
Research and identify relevant industry standards, best practices, and guidelines that are applicable to the project. These standards provide a reference for determining the acceptable level of quality.
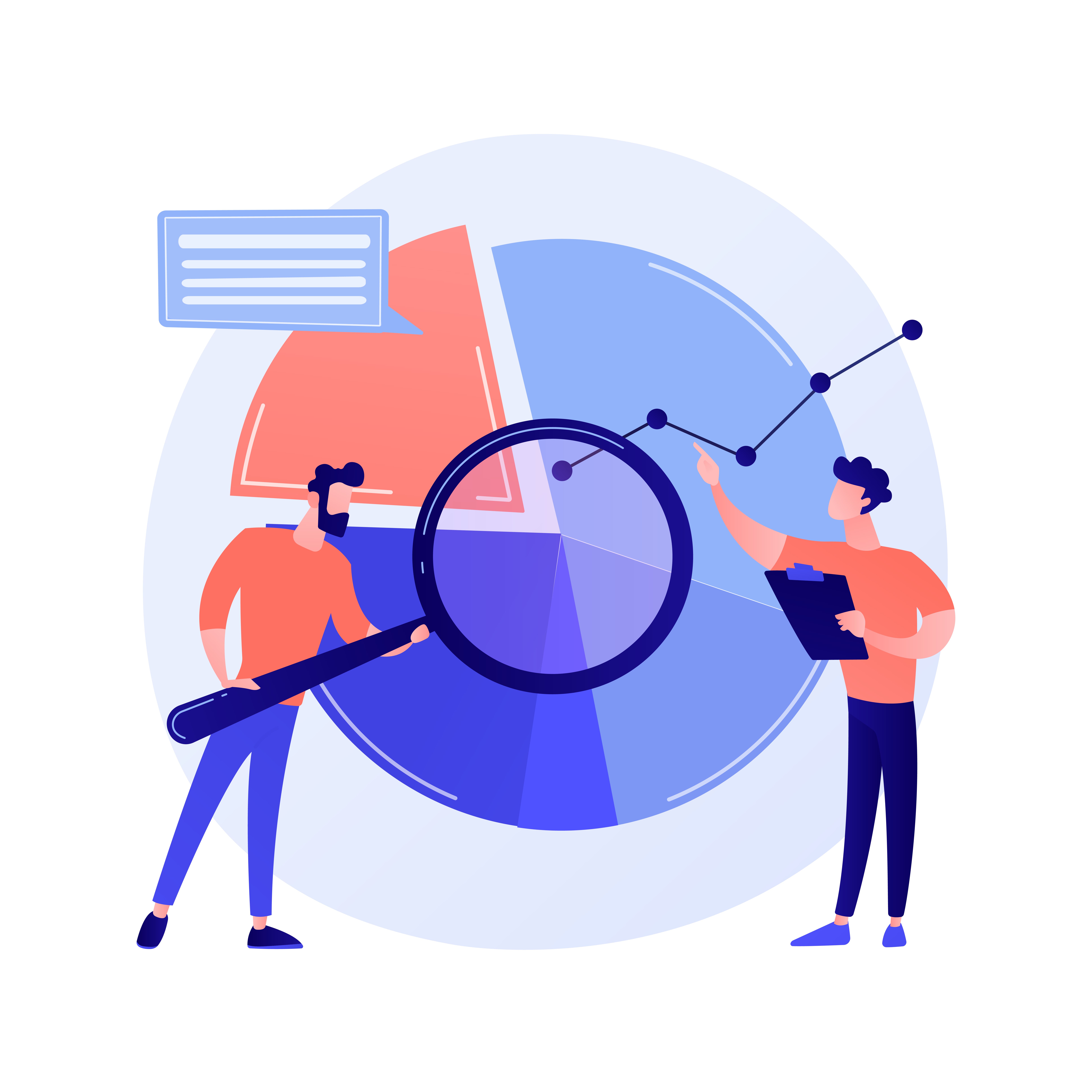
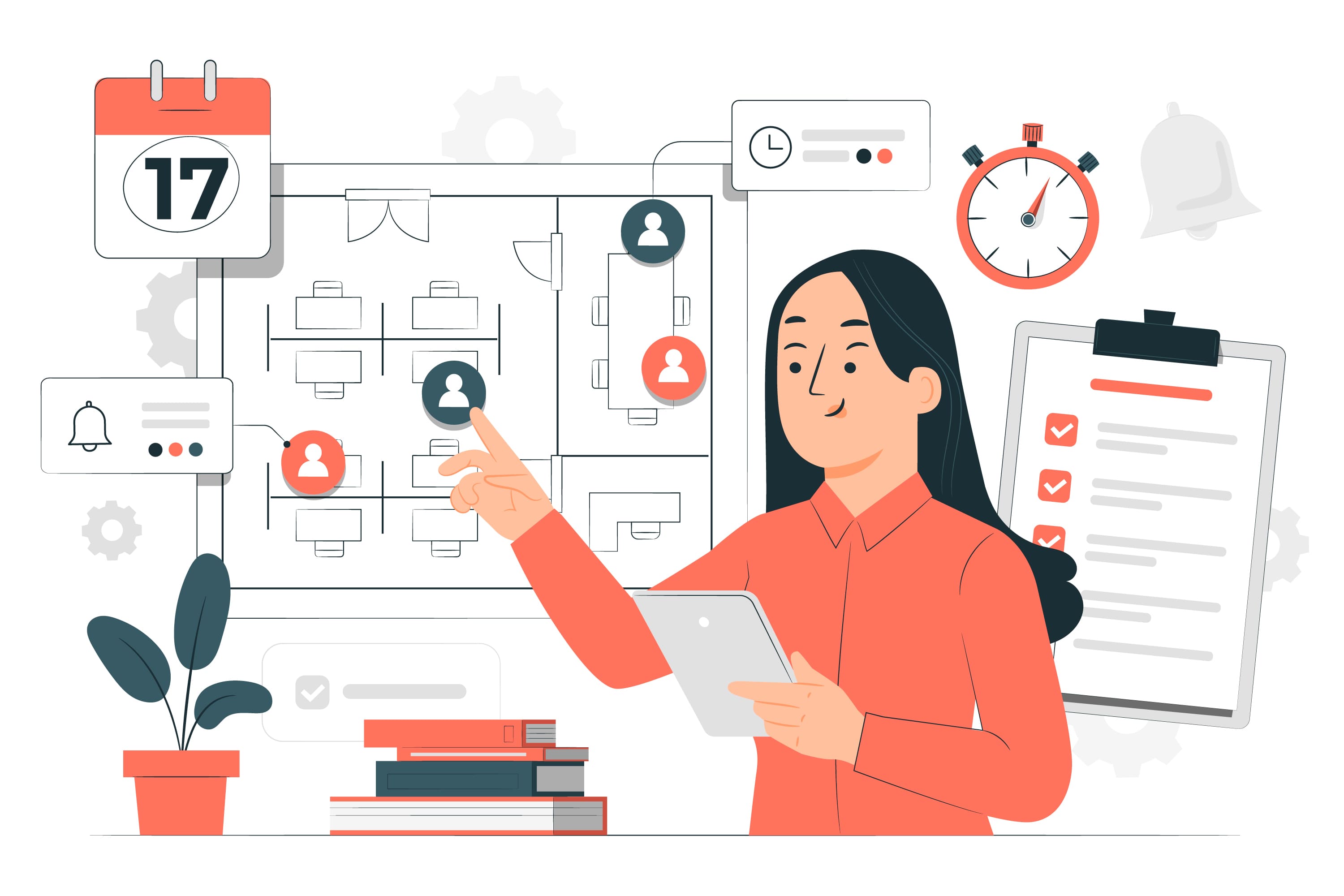
2. Establish Project-Specific Standards:
Define project-specific quality standards based on the identified quality requirements and the context of the project. These standards should be specific, measurable, and achievable within the project constraints.
3. Document Quality Standards:
Document the established quality standards, including the criteria for acceptance and rejection of deliverables, in the quality management plan. This ensures that the entire project team is aware of the expected level of quality.
Let’s consider a construction project as an example:
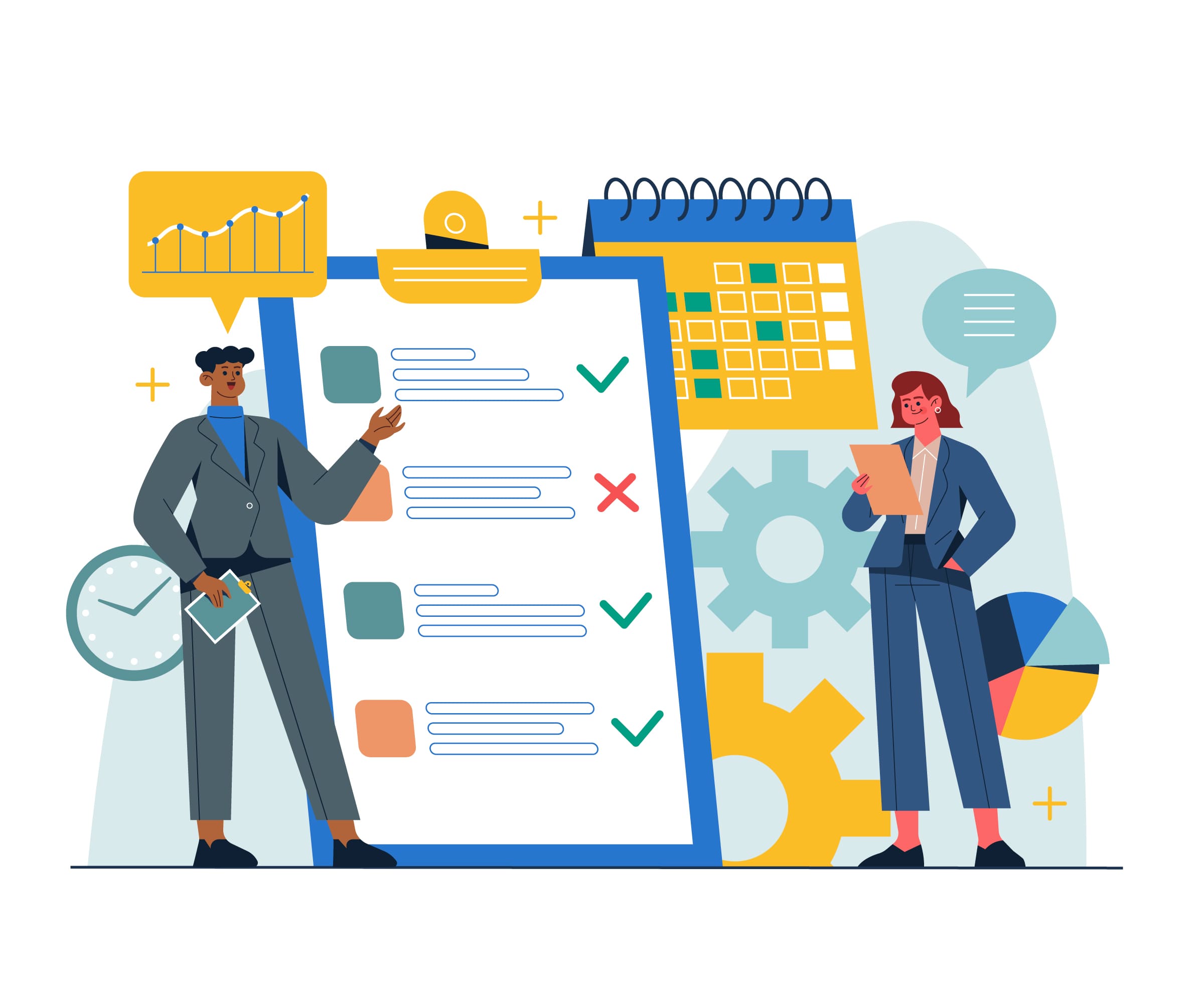
- Research Industry Standards: Research and incorporate relevant building codes, industry standards, and best practices into the project’s quality standards.
- Establish Project-Specific Standards: Define project-specific quality standards, such as the required strength of concrete, acceptable tolerances for finishes, and specifications for electrical and plumbing systems.
- Document Quality Standards: Document the established quality standards in the quality management plan, ensuring that they are accessible to the project team.
Develop Quality Management Plan
The quality management plan outlines the approach, processes, and activities that will be implemented to ensure the desired level of quality throughout the project.
Key elements of the quality management plan include:
1. Quality Assurance Activities:
Define the activities and techniques that will be employed to prevent quality issues and ensure compliance with quality requirements and standards. This may include quality audits, reviews, inspections, and process improvements.
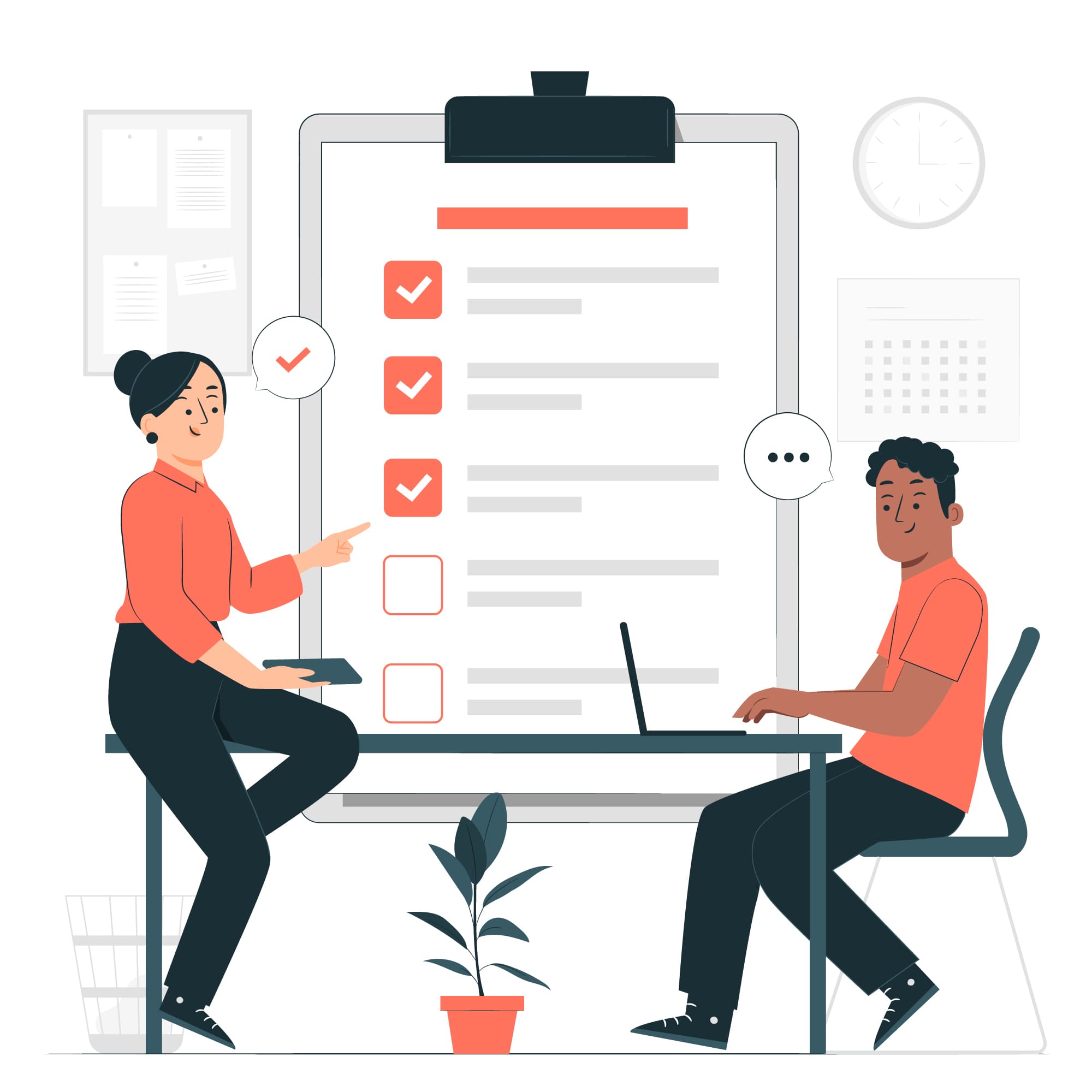
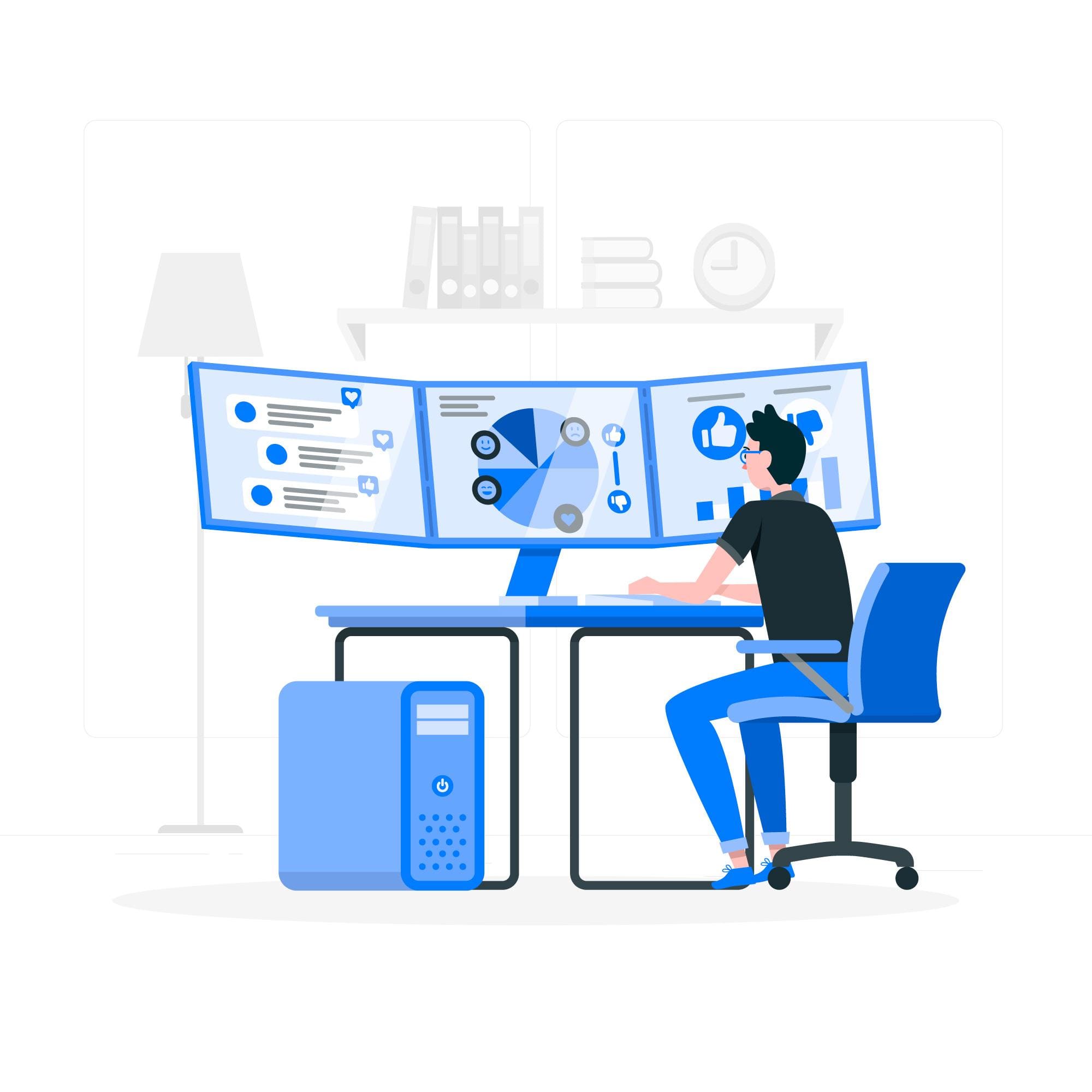
2. Quality Control Measures:
Determine the specific measures and methods that will be used to monitor and control the quality of project deliverables. This includes testing, validation, and verification processes to identify and address any quality deviations or non-conformities.
3. Roles and Responsibilities:
Assign responsibilities and roles to team members for executing quality management activities. This ensures accountability and clear ownership of quality-related tasks.
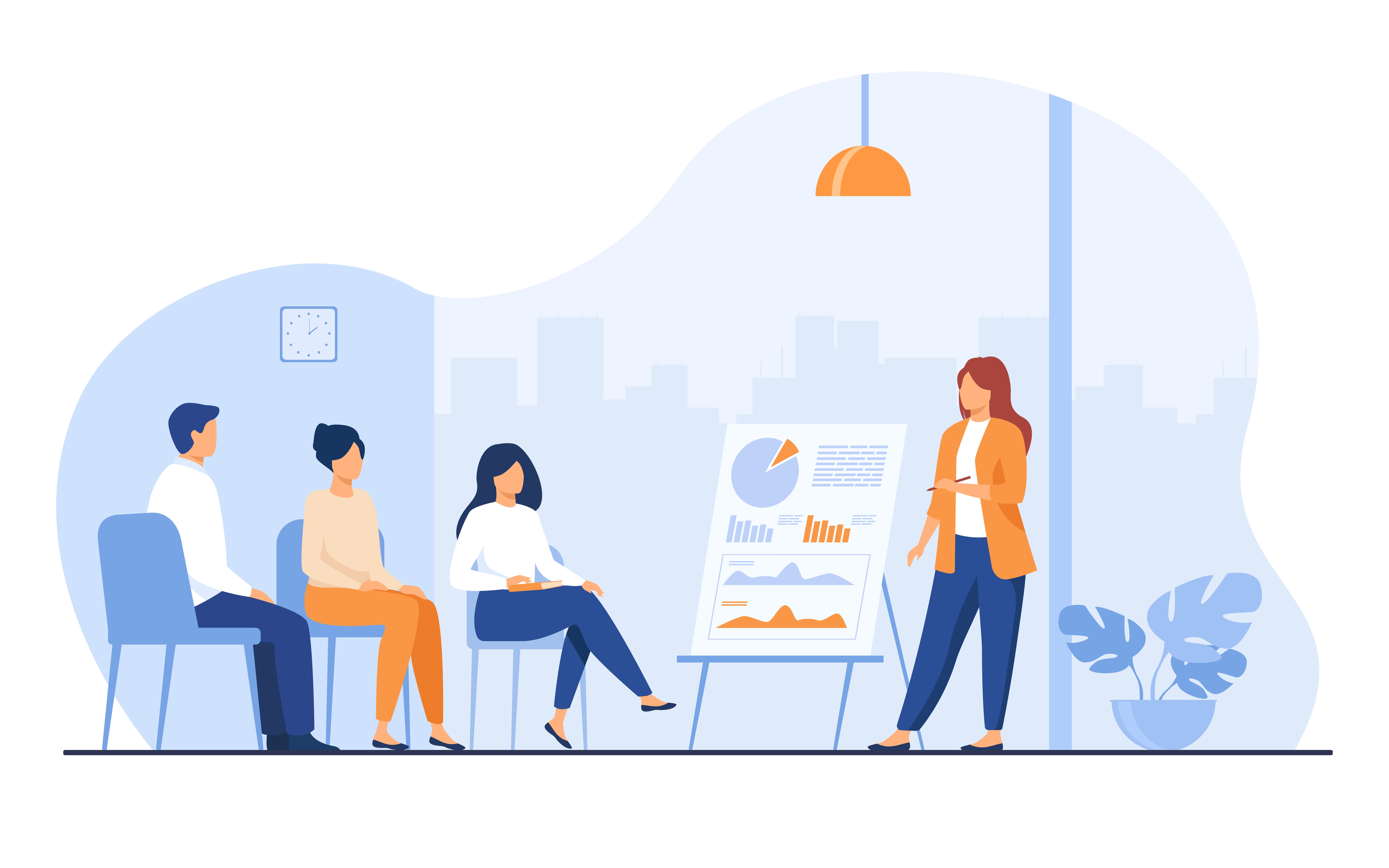
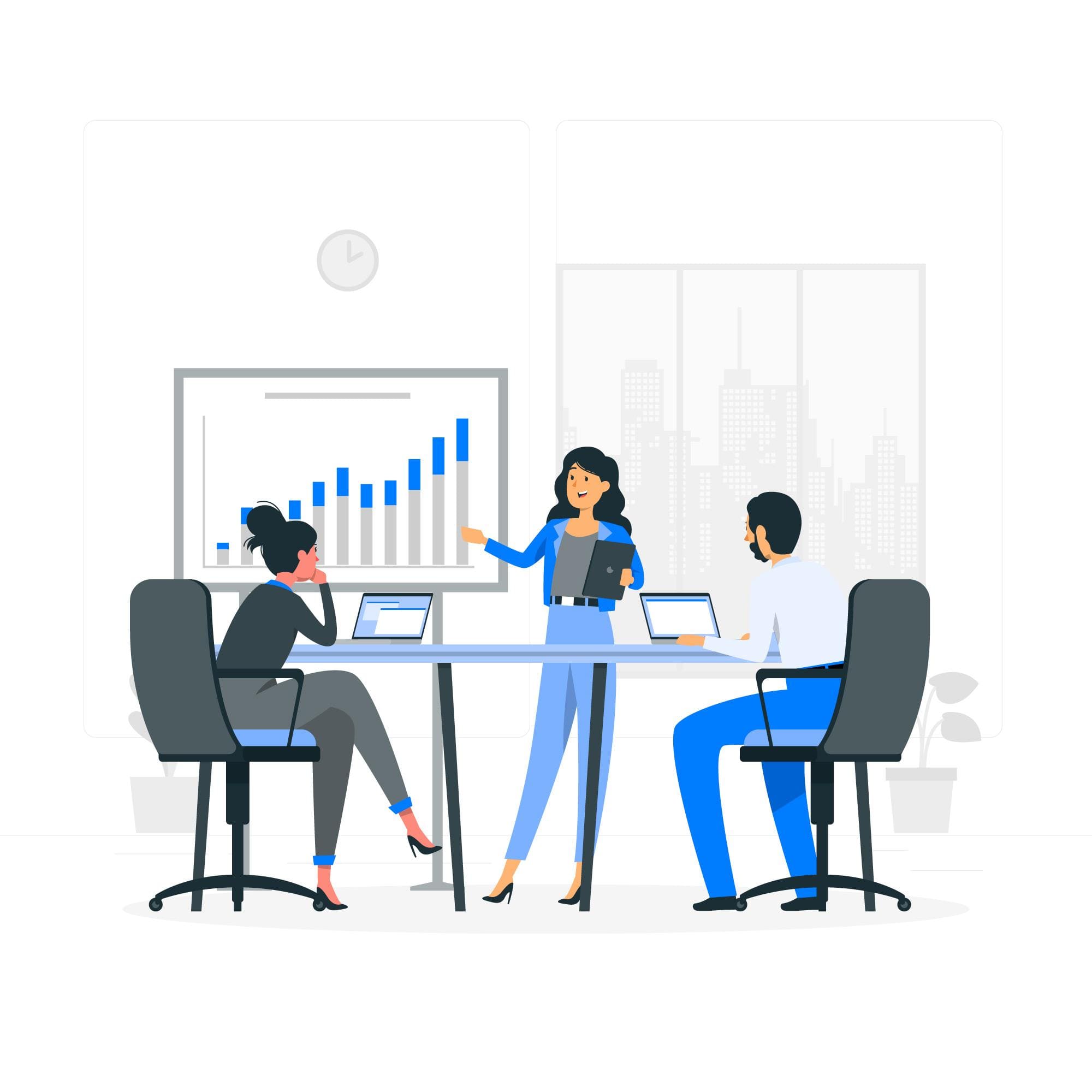
4. Quality Metrics and Reporting:
Define the metrics and parameters that will be used to measure and report on the quality of project deliverables. This enables the project team to track progress and identify areas that require improvement.
Let’s consider a construction project as an example:
- Quality Assurance Activities: Define activities such as regular inspections by qualified engineers, periodic material testing, and compliance checks with building codes.
- Quality Control Measures: Specify the procedures for conducting quality control checks, such as conducting on-site inspections, performing quality tests on materials, and tracking defects or non-conformities.
- Roles and Responsibilities: Assign responsibilities to project team members, such as the project manager, site supervisor, and quality control personnel, for executing quality management activities.
- Quality Metrics and Reporting: Determine metrics, such as the number of defects per unit area, material test results, and compliance with building codes, and establish reporting mechanisms to track and communicate quality-related information.
By following the quality planning process and developing a comprehensive quality management plan, project teams can ensure that project deliverables meet the desired level of quality, leading to customer satisfaction, compliance with standards, and overall project success.